Manufacturing has long been a cornerstone of economic productivity, driving innovation and providing countless jobs across the globe. As we step into 2025, however, one wonders if this sector can still promise the profit margins it once did. What does it take for today's manufacturing businesses to thrive?
The evolution of industry has brought about a whole new set of challenges alongside exciting opportunities. Technology is reshaping the landscape, reducing certain costs while introducing complexities. Market demands are more unpredictable than ever, influenced by global economics and socio-environmental changes. Yet, for those who are willing to adapt, the potential for profit remains substantial.
In this article, we'll explore both the challenges and the strategic pathways that can lead to continued profitability in manufacturing. We'll dissect emerging technologies, discuss the importance of sustainable practices, and highlight the need for adaptive business models. With the right approach, manufacturing can still be an incredibly lucrative arena.
- Challenges in Modern Manufacturing
- Technology's Impact on Manufacturing
- Cost Management Strategies
- Adapting to Market Changes
- Sustainable and Ethical Practices
- Future Opportunities in Manufacturing
Challenges in Modern Manufacturing
In today's industrial landscape, the manufacturing sector faces a bevy of challenges that can impact profitability. One of the most pressing issues is the rapid pace of technological advancement. While these innovations promise increased efficiency and cost savings in the long run, integrating new technology into established systems is often complicated and expensive. Many manufacturers find themselves in a difficult position, needing to invest heavily in tech upgrades just to stay competitive. This is especially true with the rise of artificial intelligence and automation, which require significant upfront investment and skilled personnel to maintain. Yet, without embracing these advancements, companies risk falling behind or becoming obsolete.
Another significant challenge is the fluctuating global economy. Manufacturers are not isolated entities; their success depends heavily on the stability of international markets. Economic downturns, trade wars, and political instabilities can drastically affect supply chains and demand for produced goods. For businesses operating on thin margins, even minor interruptions can lead to substantial financial losses. This uncertainty necessitates that manufacturers maintain strong risk management strategies and ensure a level of operational agility to adjust quickly when conditions shift. Additionally, resolving logistical challenges can be a considerable hurdle, with the supply chain disruptions that have become more commonplace in recent years.
The World Economic Forum has stated, "In the next decade, business leaders in manufacturing must navigate a complex array of challenges to remain viable. Market trends, technology adoption, and skilled workforce development will be critical."
Moreover, there's an increasing need for sustainable and ethical practices. Consumers and governments alike are placing more importance on environmental and social responsibility. This shift translates to stricter regulations and increased scrutiny, especially regarding waste management, carbon emissions, and supply chain transparency. While proven beneficial in the long-term, implementing these practices can often be resource-intensive initially, affecting short-term profits. Companies are now tasked with balancing their traditional operations with sustainability efforts to maintain public trust and compliance with new regulations.
Finally, workforce challenges cannot be neglected. The manufacturing sector is experiencing a labor shortage, exacerbated by the complex skills required for modern machinery and advanced technologies. Younger generations may be less inclined to pursue careers in manufacturing, perceiving it as less glamorous than tech or finance. Companies are thus encouraged to invest in training programs and make a compelling case for the attractive career paths the manufacturing industry can offer. A strategic focus on education and workforce development will be necessary to cultivate the talent needed to manage tomorrow's sophisticated manufacturing environments.
Technology's Impact on Manufacturing
In today's fast-paced world, technology is revolutionizing the manufacturing industry in ways that were unimaginable just a few decades ago. The incorporation of advanced technologies like automation, artificial intelligence, and the internet of things has brought about a seismic shift in how products are made, transforming the very essence of industrial production. Manufacturing processes have become more efficient, leading to reduced operational costs and increased quality of output. The use of robotics, for example, allows for precision and speed that human hands simply cannot replicate, leading to a drastic reduction in errors and waste. These efficiencies not only cut expenses, but also improve profit margins dramatically. Yet, it’s not all about the machines; human oversight and creative problem-solving remain essential components.
One cannot ignore the role of data in shaping modern manufacturing strategies. Real-time data collection has empowered manufacturers with insights that were previously out of reach, enabling them to make informed decisions swiftly. Sensors and smart devices in factories gather vast amounts of data, which, when analyzed, reveal patterns and suggest improvements for streamlining operations. This predictive maintenance capability helps businesses reduce downtime, saving both time and money. According to a report by McKinsey & Company, predictive maintenance can reduce breakdowns by 70% and decrease maintenance costs by up to 25%. Companies that embrace such innovations stand to gain a competitive edge in their quest for manufacturing profitability.
"The best manufacturing plants are those that harness data to anticipate problems before they occur," says Karen Burns, a leading industrial strategist. "Technology enables this foresight and transforms it into tangible financial benefits."
Another trend reshaping the industry is the adoption of sustainable, energy-efficient technologies. With increasing pressure to address climate change, manufacturers are seeking ways to reduce their carbon footprint. Green manufacturing technologies, such as renewable energy systems and sustainable materials, not only help businesses comply with regulatory demands but also cut long-term energy costs. Consumers today are more inclined to support businesses that prioritize sustainability, and this shift is encouraging for ethically-minded manufacturers. By committing to eco-friendly practices, manufacturers can attract a more extensive and loyal customer base, boosting their bottom line.
Moreover, 3D printing, or additive manufacturing, is increasingly making headlines as a cutting-edge innovation with the potential to disrupt traditional manufacturing norms. This technology facilitates on-demand production, massively reducing the need for inventory and associated storage costs. Products can be customized quickly and efficiently to meet specific consumer needs, eliminating the delays typical of conventional manufacturing processes. The agility offered by 3D printing is invaluable in industries where quick turnaround is paramount, opening exciting new avenues for profit ideas.
For businesses eager to stay ahead, mastering these technological advancements is no longer optional; it's imperative. As technology continues to advance, the only constant will be change itself. Companies must remain adaptive, willing to embrace new tools and methods as they arise. It's this adaptive mindset that will enable manufacturing companies to not only survive but to thrive in an ever-evolving marketplace.
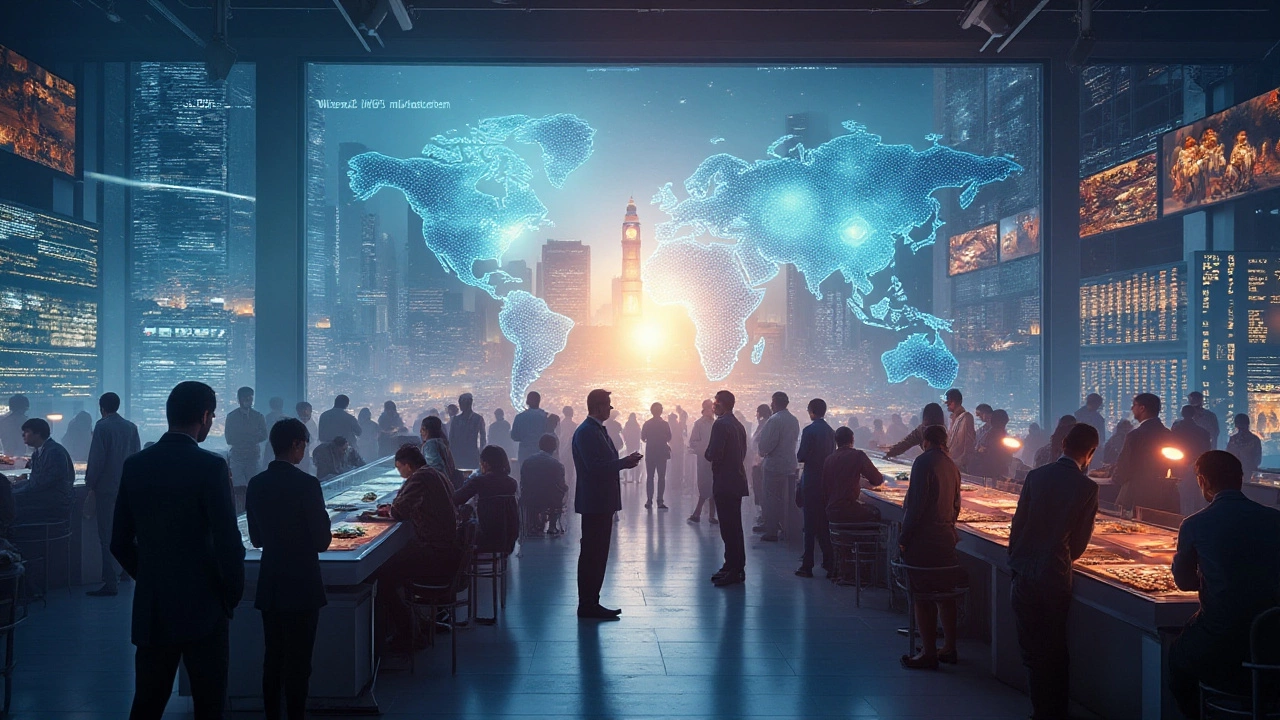
Cost Management Strategies
In the dynamic realm of manufacturing profitability, effective cost management remains a pivotal element for sustaining a competitive edge. As costs across various manufacturing stages escalate, strategic management becomes central to the profitability of any business. For many manufacturing firms, the challenge lies not just in cutting costs, but in optimizing them to boost efficiency without compromising quality. A comprehensive understanding of cost management strategies can significantly enhance the profitability of industrial production endeavors.
One of the most decisive aspects of cost management is leveraging technology. Automation and digitalization have opened avenues for reducing overheads by minimizing human error and increasing throughput. Investing in contemporary machinery and software might seem expensive initially; however, the return on investment over time often outweighs these costs. Streamlined operations brought about by automation not only cut down on labor costs but also enhance precision, potentially reducing material wastage and thus saving money in the long run.
Besides technology, supply chain optimization is critical. Building strong relationships with suppliers can lead to bulk purchasing discounts and more favorable terms, directly impacting material costs. Engaging in strategic negotiations can also ensure cost savings on logistics. Coupled with just-in-time inventory management, firms can significantly cut down costs tied to storage and inventory holding, paving the path to sustained profitability.
Energy management is another avenue often overlooked. Manufacturing facilities consume substantial amounts of energy, so implementing energy-efficient practices can lead to substantial savings. Shifting towards renewable energy sources or enhancing insulation in facilities can reduce utilities costs significantly. Moreover, many governments offer incentives for businesses that invest in green technologies, a prospect worth exploring for any forward-thinking leader in the manufacturing field.
"By adopting strategic cost management through efficiency improvements and waste reduction, manufacturers can realize a direct impact on their bottom line," says Dr. Amanda Lee, a leading expert in manufacturing systems at the University of Michigan.
Human resources management also plays a role in maintaining and improving manufacturing profitability. Investing in employee training ensures that the workforce is not only proficient in utilizing new technologies but also empowered to contribute to process improvements and innovation. A motivated and satisfied workforce can enhance productivity and reduce turnover, which subsequently leads to savings on recruitment and onboarding processes.
Let’s not forget the often subtle but significant benefits of outsourcing non-core activities. Many companies discover that outsourcing certain functions, such as IT support or logistics, can lead to a more flexible cost structure. This enables companies to divert resources toward their core competencies, ensuring focused spending where it truly counts. By embracing these cost-management strategies, industrial production ventures can unlock hidden profitability potentials, allowing for sustained growth and success in a demanding market.
Adapting to Market Changes
In recent times, the manufacturing industry has witnessed rapid and often unpredictable market changes. These changes are driven by numerous factors—advancements in technology, globalization of markets, consumer preferences shifting toward sustainability, and even political landscapes impacting trade policies. The capacity to anticipate and effectively respond to these market variations is vital for any manufacturing business longing for sustained profitability. The importance of agility within this sector cannot be overstated. By evolving with the market, manufacturers not only preserve their relevance but can also unlock new avenues of growth.
Surprisingly, a lot of successful manufacturers leverage modern analytics and data interpretation to forecast trends and adapt their production lines accordingly. This capability enables businesses to remain proactive rather than reactive. Consider, for example, the influence of AI in modern industrial setups. The integration of AI and machine learning can assist businesses in efficiently managing supply chains by predicting demand, thereby minimizing waste and optimizing inventory. According to a study by McKinsey, industries that have incorporated advanced analytics report significant improvements in their operational performance.
Moreover, consumer preferences now highly favor companies that display a commitment to ethical and environmentally friendly practices. There are manufacturers out there who have revolutionized their operations to be more sustainable—not merely because it's the right thing to do, but because it's profitable in the long run. Leading by example, renowned enterprises such as Unilever have demonstrated that sustainability can coexist with economic gain. Through transparent processes and ethical production, companies build consumer trust, which translates into loyalty and sustained revenue.
"The greatest danger in times of turbulence is not the turbulence; it is to act with yesterday’s logic." — Peter Drucker
External market forces such as geopolitical shifts and trade policies can impose restrictions but also create untapped opportunities for those willing to innovate. During times of trade disputes, diversifying suppliers or expanding into new markets have proven to be effective strategies. The capacity to quickly switch gears is no longer optional but rather a necessity. As tariffs fluctuate and trade agreements evolve, manufacturers that have diversified supply chains and strong local sourcing strategies often fair the best.
Succeeding as a future-forward manufacturer requires openness to technology, adaptability in business models, and a commitment to understanding the rapidly shifting consumer landscape. Evaluating current operations, engaging with emerging technologies, and consistently assessing market demands will equip companies with the ability not just to survive but to thrive. By focusing on innovation and sustainability, leading companies continue to remain profitable amidst the ever-changing marketplace.
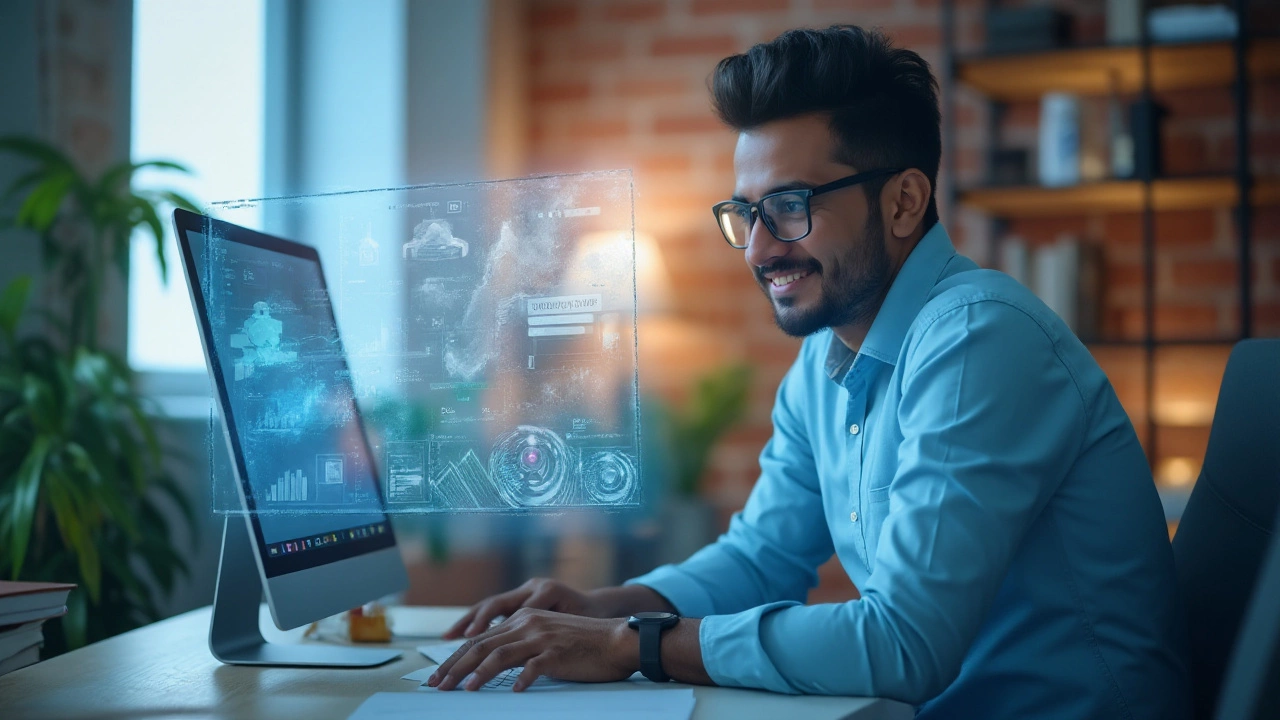
Sustainable and Ethical Practices
In today's manufacturing landscape, transitioning to sustainable and ethical practices is not just about doing what's morally right; it's a strategic move essential for long-term profitability and brand integrity. Across industries, there's a growing acknowledgment that customers and stakeholders are increasingly considering the ethical dimensions of business operations. Companies that embrace sustainable practices can differentiate themselves in crowded markets, tapping into green consumerism and attracting environmentally conscious investors.
One significant step toward sustainability is minimizing waste in the production process. Waste reduction not only contributes to environmental conservation but also translates into efficiency and cost savings. By implementing lean manufacturing techniques, businesses can optimize resource use and reduce landfill contributions. According to a report by the Ellen MacArthur Foundation, the transition to a circular economy could generate $4.5 trillion in economic benefits globally by 2030. This demonstrates both the environmental and financial potential of adopting sustainable models.
Energy efficiency is another critical component of sustainable manufacturing. Transitioning from fossil fuels to renewable energy sources can dramatically cut costs and reduce a company’s carbon footprint. With the increasing affordability of solar and wind technologies, more manufacturers are harnessing these resources to power their operations. In 2023, National Grid reported that the cost of renewable energy had dropped by 10% year-over-year, which is a compelling incentive for businesses to make the switch. By doing so, companies not only align their operations with global climate goals but also improve their profit margins by lowering energy expenditures.
On the ethical frontier, fair labor practices are paramount. Consumers are more aware than ever of where their products come from and the conditions under which they were made. Ensuring fair wages, safe working conditions, and respecting workers' rights across the supply chain builds a positive brand image and fosters customer loyalty. Nike, for example, has committed to eradicating forced labor and improving factory conditions worldwide, showcasing an industry-leading approach to ethical manufacturing.
Integrating sustainability into a company’s ethos requires fostering a culture of responsibility at every level. This involves training employees to adopt new practices and encouraging innovation in product design that prioritizes eco-friendly materials. By promoting a shared vision of sustainability, businesses can inspire employees to contribute enthusiastically to these goals, enhancing both morale and productivity. Some companies report increased talent retention and attraction due to their strong environmental commitments, highlighting another avenue through which sustainable practices can drive profitability.
"Sustainability is no longer about doing less harm. It's about doing more good." – Jochen Zeitz, Former CEO of Puma
Incorporating sustainable and ethical practices doesn't have to be overwhelming. Companies can start small, focusing on local changes and gradually scaling their efforts. Regular assessment and transparency about progress and challenges help maintain accountability and trust with stakeholders. As the manufacturing sector continues to evolve, those who leverage sustainability will find themselves not only contributing to a better world but also reaping the economic benefits of a forward-thinking approach.
Future Opportunities in Manufacturing
The landscape of manufacturing is rapidly shifting, making way for a spectrum of future opportunities that could redefine success in this sector. Driven by cutting-edge technology and changing consumer demands, businesses must remain vigilant and adaptable to seize these opportunities. Today's manufacturers are confronted with a market eager for customization, emphasizing the need for agile manufacturing solutions such as additive manufacturing and 3D printing. These technologies don't just enable customization but also facilitate rapid prototyping and enhance production efficiency. In doing so, they open doors for niche markets that were previously inaccessible, allowing for greater manufacturing profitability through personalized products that command premium pricing.
One cannot overlook the role of digital transformation in future-proofing manufacturing enterprises. The integration of IoT devices and AI-driven analytics is offering unprecedented insights into production processes, enabling businesses to optimize operations and reduce waste significantly. Digital twins, precise virtual replicas of physical entities, are becoming more commonplace, allowing manufacturers to simulate and forecast potential outcomes, thereby minimizing risk and unplanned downtime. According to a Deloitte industry report, "By 2025, businesses can expect to see as much as a 15% reduction in operational costs through smart manufacturing technologies." This is undoubtedly a compelling argument for investing in digital infrastructure as part of strategic planning.
In addition to technological advancements, sustainability presents another vital avenue for growth. Manufacturers are beginning to recognize the importance of sustainable practices, not just as a regulatory compliance measure, but as a potential competitive advantage. Environmental consciousness is increasingly influencing consumer behavior, and brands that demonstrate a commitment to reducing their carbon footprint and sourcing materials responsibly are positioning themselves for future success. With policy shifts towards greener practices, manufacturers can harness this trend to innovate, reducing energy consumption and embracing circular economy principles. Tesla, for example, has not only revolutionized the automotive industry with electric vehicles but also set an aspirational benchmark for sustainable manufacturing.
As global dynamics evolve, manufacturing businesses have opportunities in reshoring and localizing supply chains, which are becoming strategic imperatives in the wake of the recent supply chain disruptions witnessed worldwide. Resilient and localized manufacturing not only mitigates risks associated with global logistics but also taps into the growing consumer desire for "made local" products. This not only cushions against international uncertainties but also stimulates local economies, encouraging a virtuous cycle of economic benefits. The era where globalization dictated cost-cutting strategies is transforming to prioritize agility and local responsiveness.